|
THE EVOLUTION OF THE TONE BELL™ TONE RING SYSTEM
Please read the addendum at the end of the page before you try this.
I have always liked the sound that Earl Scruggs' banjo had on the Foggy Mountain Banjo album. When I first heard it, I did not realize that there was a lot of reverb on the album, but I didn't let that stop me from trying to achieve the goal I had in mind, which was to duplicate that sound.
I tried all sorts of things. I changed brands of banjo, I used different strings. I was always just a little bit away from what I was looking for. As I tell you this, bear in mind that I did not have much money to work with. I was still in college, and earned all my money playing gigs and teaching guitar and banjo.
The key came to me in 1966 in a letter from Davis Kennedy, who was a luthier and banjo technician for the Gibson plant in Kalamazoo. He described a method of altering the banjo rim itself.
First, let's look at the normal Gibson banjo body in cross section. The parts should fit snugly, with no play, as in this illustration. (For more clarification of the correct fit, see my web page on the correct fit of all the parts.)
THE STANDARD GIBSON MASTERTONE™ BANJO BODY
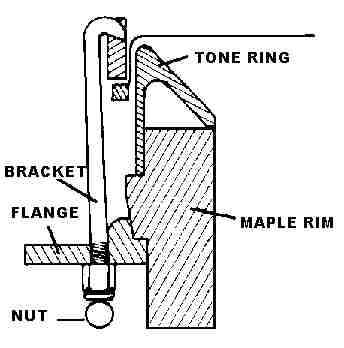 Davis Kennedy's modification was to open up the tone chamber and have a larger internal resonation chamber within the rim itself. When he described this to me, he cautioned me that it would void the warranty on the rim, so I would be doing it at my own peril! There is a lot of strain placed on the shoulder of the banjo rim between the flange and the under edge of the tone ring.
THE DAVIS KENNEDY MODIFIED TONE CHAMBER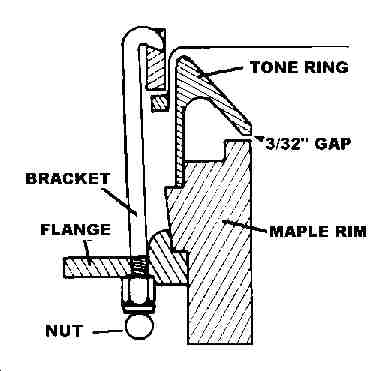 In 1969, I bought a prototypical Mastertone which had bowtie inlays, a fiddle shaped headpiece and mandolin frets. There were relatively few of these made. It was pretty good, but the tone ring was a piece of die cast junk! I ordered a tone ring from Stewart-MacDonald. This had no holes in it, but it sounded a little better than the original Gibson ring. I began to analyze the situation, and I realized what part of the problem was. The chamber inside the tone ring did not communicate with the outside world. It was a dead air space. Dead air is an insulator. It is what makes acoustical tile work. If you seal off the sound hole of your guitar, it muffles the sound. The sound was there, but it couldn't get out. Or so I thought.
Then I remembered the letter from Davis Kennedy. I took the banjo to a friend of mine who turned wooden columns for a living. His name is Jim "Lee" Morgan -- former owner of Colonial Column Manufacturing. I figured he could put the rim on one of his lathes and do the work I wanted. He came up with a much simpler solution. He used a router with a 3/8" corner round bit to round off the inner edge of the wood rim. Now the edge of the tone ring would be able to vibrate like a bell. The following illustration shows the result.
THE BILL PALMER TONE BELL™ BANJO BODY
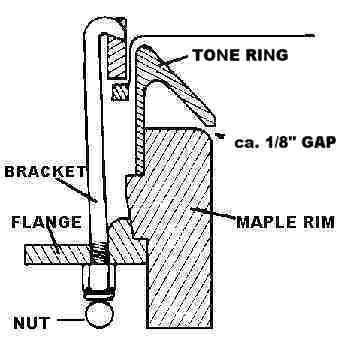 Well, the difference was amazing. The fellows I worked with couldn't believe it was the same instrument. We played with amplified instruments, and I played the banjo over a mike. This was the best 5-string banjo I have ever touched. It had lots of bass, lots of treble, and it would sustain a note for a long time--for a banjo. And it was LOUD! And it sounded a lot like Earl's banjo on that album!!!
WARNING--Do not do this yourself unless you understand that in doing so, you will render any warranty you have from the factory absolutely null and void. If you must try it, get a new banjo rim from one of the many banjo suppliers such as Janet Davis, First Quality or Stewart-MacDonald and use it as your experimental banjo rim. I will not accept responsibility for any damage you do to your instrument. Remember this when the router slips!
This is, in my opinion, a last resort. Do not do this modification unless you have tried every other possibility. Do it at your own risk.
In 1986, I sent a letter detailing this banjo's construction to Frets magazine, and part of the letter appeared in Roger Siminoff's column (December, 1986). He indicated that he didn't believe me, because, after all, volume is a subjective thing, etc. Unfortunately, there was no way I could prove my point, because, to my deep regret, I had sold the banjo. I wish I hadn't. Roger misunderstood the point about dead air being an insulator--saying that air was a conductor--after all, we heard our sounds through the air. Well, he was right, up to a point--air does conduct sound; however, dead air is an insulator. It is the stuff in acoustical tile that provides the insulating qualities. In fact, the sounding boards of various instruments and their tone chambers serve the purpose of moving more air than a naked string, so we can hear the sounds of our instruments.
In late 1996, I got the "bug" again, and purchased an Epiphone Masterbuilt banjo. Not bad for the money, but NOT a Mastertone. So I found a Buck tone ring which is similar to the old Stewart-MacDonald ring, and when I installed it--BINGO! There was the sound once more.
During the coming several months, I will be trying various tone ring, rim and flange combinations to see what differences I can detect in the construction of these banjos. Most people that I have talked to about this system have been helpful or even encouraging. A few have dismissed my theories as somewhat "on the edge." But none of the nay sayers has played my banjo.
ADDENDUM--JANUARY 6, 1997
Tone Bell™Test Results Posted on the Internet
The tests of the Tone Bell™ system are now underway. I am testing this system using as many of the popular and easily available tone rings as possible. To see the results of these experiments as they progress, click here.
Those who have played it have all been impressed with the volume and the tone. Heifetz once said, "Give me a violin that's loud, and I'll put the tone into it!" Well, my Tone Bell™ system gives you both!
WARNING!!!!
Do not try this modification if your banjo has an aluminum tone ring. Bailey Henry of Florida tried this with an Alvarez Denver Belle which had an aluminum tone ring. The tone ring collapsed. Aluminum has some big disadvantages in construction.
ADDENDUM--FEBRUARY 25, 1997
I recently received a piece of e-mail from Mr. Toshiro Asano of Niigata, Japan. In this e-mail, he pointed out that this tone ring mounting system had been mentioned also in the February 1975 issue of Banjo Newsletter magazine. Don Branhan, who was appparently living in Sapporo, Japan at the time described two Japanese instruments that he had seen, one by Bluebell and the other by Tokai. The Bluebell banjo had a Mastertone-style tone ring that was mounted on a wooden rim in such a way that the inner edge was clear of the rim by .025" according to the letter. The Tokai had the same system, but also included a circular round brass ring that rested inside the Mastertone-type ring. These particular instruments were not available in the US when I was conducting my first experiments. However, shortly after I created the first Tone Bell ™ banjo, I saw some instruments by Alvarez that were similar to the Tokai instruments.
The clearance of the tone ring on its inner edge was more like .25" , so perhaps we are dealing with a typographical error here. I saw my first Alvarez in 1970. I found that these banjos sounded better when the inner brass ring was removed, leaving only the Mastertone-type tone ring. There was a pair of major differences in these banjos and the Tone Bell™ instrument. That was the thickness of the rim and its mass. The heavy 3/4" rock maple rim of the Gibson instrument contributes much to the bass response and sustain of the banjo. Those who have played the old aluminum bodied flathead Ode instruments will know of what I write. They were very bright, but did not have the bottom end necessary for really good bluegrass work. The wooden bodied Alvarez instruments sounded better to me than the old flathead Ode banjos, but were still quite bright. Mr. Branhan mentioned in his letter that the Tokai and Bluebell instruments sounded brighter than his Mastertone. This would be consistent with my findings.
In the 1970's the Japanese musical instrument manufacturers had taken to attending musical instrument manufacturing conventions. They would wear a tie tack which measured 1 cm. on a side. They would pose either holding or standing next to an instrument they desired to copy and have their pictures taken. The photos would be blown up to full size using the tie tack as a reference point. Later, these instruments would appear on the market as excellent external copies. However, the internal structures often left much to be desired.
Several American manufacturers including Slingerland, Bacon & Day, Leedy & Ludwig have manufactured banjos with free hanging tone rings, but none of them had the massive Gibson maple rim.
Thanks, Mr. Asano, for pointing out this bit of information.
A Key Factor in the Sound of a Banjo
and How You May Be Able to Acquire it More Quickly
In a recent (May 8, 1997) post to Banjo-L, the general listserver for banjo enthusiasts of all types, Sonny Osborne made several comments about pre-war mastertone banjos. I will not quote him here, but basically he said that none of the modern banjos have the sound of the old ones. I have played some of these old banjos, and he is right. They do have a sound that is difficult, if not impossible, to get out of a new instrument. However, in my opinion, the new banjos are by no means hopeless. Most of them can achieve a sound very similar to the better old banjos by adjusting them correctly and making sure that everything that can be done to make the instrument sound good is done to it.
The one factor that cannot be duplicated is the age of the instrument. Of the half dozen or so instruments he listed as being the best of the bunch, all of them have been played fairly constantly for several decades. This means to me that the banjos have been "worked in." Fine instruments of all types improve with age. Inferior instruments do not. Possibly the exception to this are some of the extremely delicate classic and flamenco guitars, which seem to wear out after a couple of decades. Banjos, however, are not that delicate!
Fine instruments must be played. This is true for violins, banjos, guitars--all instruments. There are groups who tour with the Stradivarius violins that are in several museums, just to make sure they maintain their ability to vibrate properly. A friend of mine who played the classic guitar told me of a method his teacher used to break in a new guitar. He would place the guitar in a stand in front of his stereo and play classical guitar music through the speakers while he was at work. The theory was that the guitar would vibrate in sympathy with the music coming from the speakers, thus breaking it in a bit more quickly. Try this with your banjo--it couldn't hurt!
For further information, or to comment on how crazy this system appears to be, please send e-mail to: Bill@billpalmer.com
If you are a builder or manufacturer of banjos and you would be interested in using the Tone Bell™ system in your instruments, click here.
Copyright 1996, 1997 by Bill Palmer. All manufacturing rights reserved.
Janet Davis Now Manufacturing Tone Bell™ RimsFor more information, click here
Addendum -- added 05/09/2006
Today, I got an e-mail from a disgruntled reader who has told me that he thinks the Tone Bell™ system is basically bunk, and challenging me to put up all the e-mails from people who have ruined banjo rims by trying out the Tone Bell™ system.
The only negative feedback I have gotten is from Bailey Henry. That information is posted above. I believe that I have emphasized in the first few sections of this page that
1) This should never be done on an original equipment rim.
2) There is risk involved (as in "do this at your own risk"
3) It is a last resort.
I would also like to point out that every time anyone has e-mailed me about doing this modification, I have tried to talk him out of it. It is pretty obvious that once you have taken the wood off the inside edge of the rim, that you will have made a non-revrsible modification to it. Well, actually, that's not entirely true. You could have someone add a layer of maple to the top of the rim, and restore it that way. But the idea of permanently altering your rim is one that I have discouraged from day one.
\
Why would I misrepresent this, anyway? I have nothing to gain from it. I don't charge for it. I'm not even paid a royalty by anyone who manufactures Tone Bell™ rims. You can't see them from the outside of the banjo.
If you have actually ruined a rim by doing a Tone Bell™ modification to your rim, and you took all the advice I gave above, please send me an e-mail by clicking on this link. bill@billpalmer.com. Include the exact steps you took, including copies of any e-mails you sent me about the steps you were going to take and the answers I sent you. I will post them here.
I don't see how I can be any fairer than that.
But if you did not follow the steps exactly as I outlined, and you did it to an original rim, you didn't follow my advice, and I will not be responsible for anything that you did to your banjo.
A final note about the Tone Bell™ system.
I mentioned above that I had sold the banjo that I performed the original modification on. This was an instrument that I purchased in 1969, and I used it for several years after that. I sold it to one of my former banjo students, Tom Reid.
Tom played this banjo all over the place. He went to a lot of bluegrass festivals in Texas and other places. Tom passed away a couple of years ago. When I learned of this, I called his widow and asked if she would like for me to purchase the instrument. She said that she had been hoping I would call.
I got the banjo back right after SPBGMA 2007. I sent the parts to Paul Hopkins for refinishing, because there was a lot of damage to the original lacquer surface. I had him remove the Vega 5th string capo and repair the holes in the binding. The tone ring and rim were still in excellent shape.
The tone ring looks like one that was made by Steve Ryan. I have heard that Steve made some tone rings for Stew-Mac back then.
I sent the metal parts to Nashville Plating Service to have them replated. Tony Pass got the rim and made me a Tony Pass rim to match the old one. I decided to use a Hopkins Full Flathead tone ring in the instrument. I had Nashville Plating Service replate it in chrome.
This banjo is formidable. It has a pleasing tone, lots of volume and a great action. I firmly believe that the Tony Pass rim has made the Tone Bell™ system obsolete.
Gibson, Epiphone, Mastertone and Masterbuilt are registered trademarks of Gibson, USA.
Fender is a registered trademark of whoever owns Fender, Inc. now--could be CBS!
Vega is a trademark of Deering.
Go back to Banjo Setup
Go back to My Music
©2006 Bill Palmer. All rights reserved. For permission to republish contact Bill Palmer. The opinions expressed on this page are strictly Bill Palmer's. Mastertone, Stelling and the other brand and model names are the property of the manufacturers and other people who own them.
| |